Step-by-Step Guide to Prevent Main Shaft Fracture in Jaw Crushers and Impact Crushers
- Prakash Agarwal
- Jul 31, 2024
- 3 min read
The fracture of the main shaft in crushers can lead to long maintenance times and high costs, causing significant economic losses for businesses. Understanding the reasons behind main shaft fractures and implementing preventive measures can help mitigate these risks and ensure continuous production.
Step 1: Understand the Reasons for Main Shaft Fracture

For Jaw Crushers:
Performance Issues
Ensure proper heat treatment during manufacturing to enhance fatigue resistance. Crushing high-hardness materials or those that can't be crushed increases resistance and can burden the main shaft, leading to fractures.
Speed Control
Avoid large fluctuations in engine speed due to load changes. Both large and small fluctuations can destabilize the crusher, increasing wear and the risk of main shaft fractures.
Operational Practices
Avoid sudden increases in feed volume or changes in material properties, which can cause temporary loss of control and accelerated wear on the main shaft.
Structural Design
Ensure reasonable structural design with adequate mating surface interference, sufficient fillets, and unloading grooves to prevent stress concentration and fatigue. Call 824093968 to get a quote for Jaw Crusher
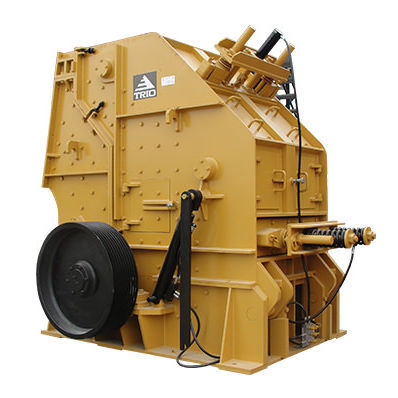
For Impact Crushers:
Material Quality and Heat Treatment
Use high-quality materials and proper heat treatment to prevent stress concentration, cracking, and fractures.
Production Operation
Avoid feeding large, non-crushable objects like iron, which can cause severe wear and fractures. Prevent long-term overloading, which impacts the main shaft and leads to fractures.
Lubrication
Ensure proper lubrication to maintain the service life of the main shaft. Moisture in lubricating oil can reduce oil film thickness, accelerating crack expansion and causing fractures.
Call 824093968 to get a quote for Impact Crusher
Step 2: Implement Preventive Measures
Enhance Maintenance Awareness
Train operators to maintain equipment properly, ensuring the integrity of buckets, gears, transport belts, and hinged pin shafts to prevent metal impurities from entering the crusher. Conduct timely maintenance and replacement of worn parts.
Ensure Proper Lubrication
Lubricate equipment as required and check lubrication regularly. Monitor oil pressure, oil temperature, and abnormal noises during operation.
Maintain Vigilant Supervision
Supervisors should closely monitor equipment operation and remove foreign objects promptly to keep the crusher in optimal working condition.
Recycle Damaged Parts Properly
Properly recycle damaged parts and avoid discarding metal materials into the ore. Replace equipment nearing the end of its lifecycle to prevent unexpected failures.
Monitor Feeding Volume
Regularly check and control the feeding volume to prevent excessive feeding, which can cause main shaft fractures.
Conduct Regular Stress Detection
Use ultrasonic and other instruments to detect main shaft stress, understand the degree of stress, and replace worn parts promptly.
Maintain Inventory Backup
Keep an inventory of critical parts like the main shaft to avoid production stoppages during repairs.
Invest in Professional Skills Training
Provide comprehensive training for operators to enhance their practical skills, ensuring effective equipment maintenance and timely repairs.
Step 3: Invest in High-Quality Main Shafts
Preventing main shaft fractures not only saves costs but also ensures continuous production. Investing in high-quality, properly treated main shafts is crucial for the longevity and performance of your crushers.
Contact Us on 824093968 to Buy a Main Shaft
Ready to enhance your crusher's performance and prevent costly breakdowns? Contact us today to purchase high-quality main shafts tailored to your needs. Keep your crushers running smoothly and efficiently with our reliable products. Get the best prices and unmatched durability to ensure your operations stay on track.
Yorumlar