How to pick the Stone Crusher Size
- Prakash Agarwal
- Dec 24, 2024
- 2 min read
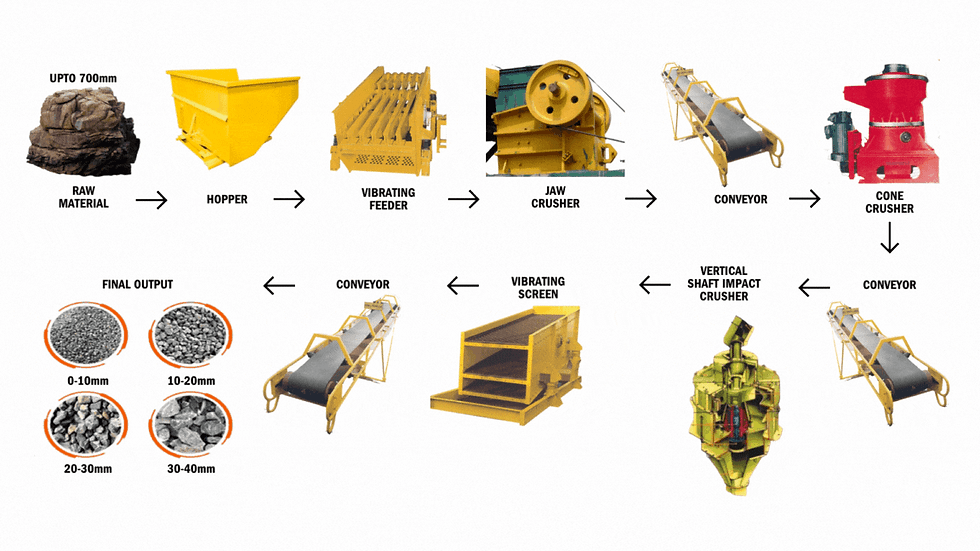
When it comes to crushing stones for various industries, choosing the right crusher can feel like solving a puzzle. After all, every stone has unique properties, and every industry has specific size requirements for its materials. Whether you’re working on a road construction project, mining operation, or producing aggregates for construction, selecting the right combination of crushers is crucial.
In this blog, we'll explore what kind of stone requires what type of crusher. We've broken it down into a simple table for easy understanding, covering input and output sizes, primary and secondary crushers, and their roles in the process.
So, let’s get started and simplify the world of stone crushing!
Industry | Stone | Input Size | Output Size | Primary Crusher Needed | Secondary Crusher Needed |
Road Construction | Basalt | 300-600 mm | 20-40 mm | Jaw Crusher 36x24 | Cone Crusher 42x8 |
Granite | 300-800 mm | 20-50 mm | Jaw Crusher 42x30 | Impact Crusher 48x10 | |
Mining | Limestone | 500-800 mm | 10-30 mm | Jaw Crusher 42x32 | Hammer Crusher 36x20 |
Iron Ore | 400-700 mm | 10-20 mm | Jaw Crusher 36x24 | Cone Crusher 42x10 | |
Coal | 200-400 mm | 0-50 mm | Roll Crusher 30x18 | - - | |
Construction Aggregates | Dolomite | 400-600 mm | 10-40 mm | Jaw Crusher 42x30 | Impact Crusher 48x10 |
Sandstone | 300-500 mm | 5-20 mm | Jaw Crusher 36x24 | Vertical Shaft Impact Crusher (VSI) 42x8 | |
Cement Industry | Gypsum | 100-300 mm | 0-10 mm | Hammer Crusher 30x18 | - - |
Barite | 200-400 mm | 0-50 mm | Jaw Crusher 36x20 | Hammer Crusher 30x18 | |
Marble Processing | Marble | 300-600 mm | 20-50 mm | Jaw Crusher 36x24 | Impact Crusher 42x10 |
Chemical Industry | Talc | 200-400 mm | 0-10 mm | Hammer Crusher 30x18 | - - |
Graphite | 300-500 mm | 5-20 mm | Jaw Crusher 36x20 | Cone Crusher 42x8 | |
Infrastructure Projects | Sand | 0-50 mm | 0-10 mm | Jaw Crusher 30x18 | Vertical Shaft Impact Crusher (VSI) 36x24 |
Granite | 300-800 mm | 20-50 mm | Jaw Crusher 42x30 | Cone Crusher 48x10 |
Crusher Pairing: Most applications require a combination of primary and secondary crushers to achieve the desired output size.
Flexibility in Selection: For softer stones (e.g., coal, gypsum), a single crusher is often sufficient, while harder stones (e.g., basalt, granite) require both jaw and roll crushers.
Sizing Matters: Proper sizing of crushers ensures efficiency and cost-effectiveness.
As we’ve seen, the choice of crusher depends not just on the type of stone but also on the industry’s specific needs. While a jaw crusher is perfect for primary crushing of large stones, secondary crushers like roll crushers and hammer crushers refine the material to meet the desired output size.
Understanding these dynamics can help you select the right equipment for your project, saving both time and money. If you’re looking for reliable and efficient jaw or roll crushers, feel free to reach out. Let’s ensure your crushing process is as smooth as possible—pun intended!
Comments